Power Generation
We have extensive experience in all types of boiler refractories ranging from small package type boilers, Fluid Bed Boilers to large fossil fired power stations up to 600 MW capacity. The main emphasis for the work associated with the smaller boilers is in relation to the burner quarls which are usually provided in a manufactured segmental form or can be rammed to the desired contour using a propriety mouldable refractory. We at Cameron Furnace can provide quarl segments cast at our factory in formers to suit any burner design.
The larger fossil fired units have a number of areas requiring a variety of different applications utilising many of the sophisticated materials available on the market place which require to be installed either by hand or mechanical means. For example the ash hearth can consist of traditional brickwork, cast concrete, gunned concrete4 and pump injected insulation, all of which can be installed to a high standard by our personnel.
A critical item within these units is the burner quarls the purpose of which is to ensure the correct flame profile from the burner whilst at the same time offering protection to the surrounding tubes from flame impingement. The integrity therefore of the installation has to be sound given the fact that each unit is expected to run trouble free for three years from one maintenance period to another. A well installed quarl can survive without major refurbishment for up to six years.
The technology of research and development over the years has resulted in the success of Silicon Carbide based materials being used for the quarl manufacture and mouldable bed and surround and in appropriate cases a concealed fixing method of quarl retention has been successful in prolonging its life expectancy. We have developed a stopper system for the bolt-through style which can give the same security as that of the hidden method.
There is no double that the utilisation of a well installed prefired silicon carbide tile will contribute greatly to the efficiency of the boiler performance resulting in economies in the burning of coal which can be over 6000 tonnes per day.
In all cases of refractory installation, the end product is only as good as the anchor system which retains it therefore we at Cameron Furnace Company pay particular attention to the design of the retention system, ensuring that the operational criteria of the unit is represented with the appropriate style of anchors.
There are a number of situations within a large boiler where access can be difficult such that mechanical means are required to transport the material from the preparation area to the job face. We have trained and skilled operatives in al gunning techniques who are able to install materials to these areas in an efficient manner resulting in economy of both time and material.
In all cases it is the policy of the Company to promote a Healthy and safe working environment ensuring that all our operatives are equipped with the appropriate Personal Protective Equipment and accompanying guidance.
Get in touch
Accreditations
We are compliant with standards in Quality, Environment and Health and Safety. Click the name of an Accreditation to the view the document.
Waste Carriers’ License
OHSAS 18001 2007 Certificate of Registration
ISO 14001 2015 Certificate of Registration
ISO 9001 2015 Certificate of Registration
Employers, Public, Products Liability Insurance Indemnity Limit
Employers Liability Certificate
FCS Cameron have many years of experience and knowledge gained within the power generation industry.
Petrochemical
Incineration
Iron & Steel
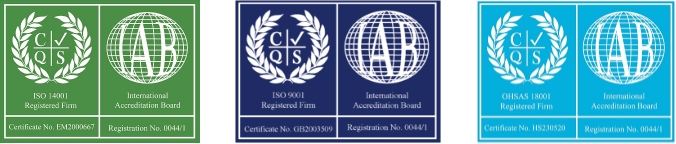